РЕКОНСТРУКЦИЯ И МОДЕРНИЗАЦИЯ МЕТАЛЛОРЕЖУЩИХ СТАНКОВ
    На большинстве предприятий Казахстана парк
металлообрабатывающих станков значительно
изношен, особенно в части силового
электрического оборудования и систем управления.
Из-за спада производства станки длительное время
не эксплуатировались, вследствие чего, многие из
них разукомплектованы. В настоящее время
предприятия возобновляют производство,
наращивают объем выпускаемой продукции, и,
следовательно, требуется обновление и
восстановление станочного парка.
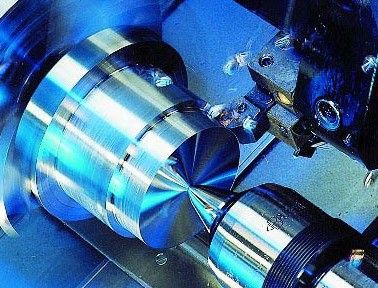
Рисунок №1
    Начиная с конца 80 годов прошлого века, станочный парк не обновлялся, имеющееся на
предприятиях оборудование находится в эксплуатации 30 и более лет. Многие станки,
особенно для обработки крупногабаритных изделий имеют регулируемые привода по
системе генератор-двигатель со схемой управления на электромагнитных или
электромашинных усилителях, а иногда даже с усилителями на электронных лампах. Эти
системы управления громоздки и не надежны, затруднен их ремонт и эксплуатация.
Наличие вращающихся машин (генератора и приводного двигателя) увеличивает
занимаемые оборудованием производственные площади, создают излишний шум,
наблюдается износ механических частей машин. При реконструкции и восстановлении
оборудования экономически и технически целесообразнее заменить существующие
системы управления на современные, разработанные с учетом последних достижений в
области электроники и микропроцессорной техники. Предлагаемое, на сегодняшний день,
для этих целей оборудование намного надежнее и производительнее. Применение его при
реконструкции и восстановлении станочного парка позволит добиться надежной работы,
довести эксплуатационные показатели станков до современного уровня развития техники
в области станкостроения.
ОБОРУДОВАНИЕ, ПРЕДЛАГАЕМОЕ ДЛЯ РЕКОНСТРУКЦИИ СТАНКОВ
    
Мини контроллеры и логические модули позволяют заменить громоздкие и
ненадежные релейные схемы управления на современные устройства с
микропроцессорной техникой.
Наибольшее распространение для этих целей получили:
- контроллеры OCS-100 и OCS-200 фирмы GE Fanuc;
- SIMATIC C7-621 фирмы Siemens.
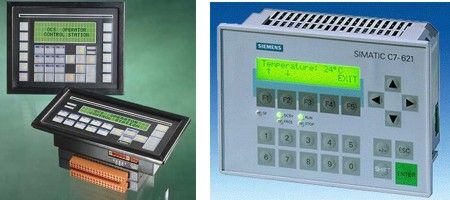
Рисунок №2
    Эти контроллеры, наряду с малыми габаритами и
относительно низкой ценной, сочетают в себе
одновременно процессор и панель оператора. Такие
контроллеры называют
«ДВА В ОДНОМ». Эти
контроллеры легко монтируются в пульты управления и
посредством буквенно-цифрового дисплея позволяют
получить сообщения о режимах работы станка,
диагностику состояния механизмов. Передние панели
контроллеров снабжены клавиатурой, что позволяет
вводить требуемые
параметры работы станка
(скорость резания, скорости подач, число проходов,
конфигурацию обрабатываемой поверхности и т.д.).
С помощью этих контроллеров можно реализовать системы
точного позиционирования, т.е. они успешно заменят такие
устройства как «РАЗМЕР М» и ему подобные. В некоторых случаях можно реализовать
простейшую систему ЧПУ. Несмотря на свои малые габаритные размеры, его
программное обеспечение позволяет реализовать всевозможные логические
преобразования, а так же выполнять математические операции над непрерывным
сигналом в цифровом виде.
При применении контроллеров полностью исключается из
схемы:
- электромеханические реле,
- усилители,
- блоки согласования и преобразования сигналов.
    По своим функциональным возможностям системы с контроллерами имеют больше
возможностей, чем схемы с электромеханическими реле, появилась возможность
расширить блокировочные связи, контролировать действия станочника, исключая и
предупреждая аварийные ситуации (человеческий фактор).
Так что это не просто замена одного вида оборудования на другое,
а это совершенно новое качество системы управления.
    Применение контроллеров позволяет снизить объем потребной кабельной продукции
для вторичной коммутации, т.к. сигналы управления передаются по линиям связи
состоящей из одной, максимум двух, пар проводов.
Меняется в лучшую сторону и дизайн пультов управления:
- сокращается число органов управления (кнопок, ключей, потенциометров,
переключателей),
- конструктивно органы управления на много проще, чем при релейных схемах
управления,
- управление станком становится эргономичнее.
На основе контроллеров нами произведена модернизация:
- Станка для шлифования валков прокатных станов. Блок управления
которого выполнен на контроллере OCS 100 и обеспечивает формирование
поверхности валка по заданной кривой.
- Линия поперечной резки рулонного металла на листы заданной длины.
онтроллер управляет скоростными режимами, мерным резом, ведет учет
производительности, формирует пачки металла с заданными параметрами.
- Вулканизационный пресс. Система управления на OCS 100 управляет
циклами вулканизации транспортерной лентой, обеспечивая
технологический процесс по заданной программе, контролирует давление
и температуру, управляет элементами мнемосхемы и вспомогательными
механизмами.
- Испытательный стенд. Стенд предназначен для испытания и обкатки
шестеренчатых редукторов генераторов пассажирских вагонов. Система
обеспечивает заданные по времени скоростные и нагрузочные
характеристики программы испытания. В памяти контроллера хранятся
несколько различных программ, а также есть возможность устанавливать
новые или корректировать ранее записанные программы.
- Пресс для производства метало-черепицы. Управление процессов
формирования заданных размеров и конфигурацией выпускаемой
продукции, обеспечивается автоматический цикл производства.
    Не все станки предназначены для выполнения сложных технологических циклов, и,
следовательно, система управления для них значительно
проще. В этом случае при реконструкции релейных схем
используются логические модули типа
«LOGO!» фирмы
SIEMENS. Об этом модуле говорят:
«МАЛ ДА УДАЛ»,
потому что в малом объеме, при низкой цене, скрыты
большие возможности. Любая релейная схема может быть полностью заменена одним
блоком, редко несколькими блоками. За счет того, что модули можно расширять по
числу входов и выходов (до 24 входов и до 20 выходов), всегда есть возможность
подобрать оптимально по цене оборудование для решения конкретной задачи.
Модуль удобен для программирования и имеет полный набор:
- логических функций,
- таймеров,
- счетчиков,
- регистров сдвига,
- частотных и аналоговых компараторов.
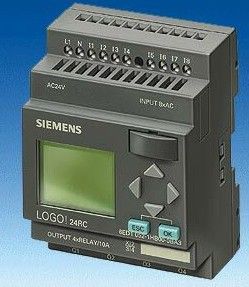
Рисунок №3
    Он может принимать аналоговых сигналов и выполнять над ними операции сравнения
посредством компараторов. На экран модуля выводятся некоторые сообщения, что
облегчает диагностику.
«LOGO!» работают в широком диапазоне напряжений, имеют
релейные выходы, что позволяет подключать нагрузку до 10 А. Эта серия
комплектуется также специальными источники питания и миниатюрными контакторами
для 3-х фазных для нагрузок до 5 кВА.
На модулях «LOGO!» выполнено:
- Управление гильотинными ножницами.
- Управление гибочным прессом.
- Управление штамповочными прессами.
- Управление прессом формовых изделий.
- Управление линией продольной резки металла.
    Особое значение имеет реконструкция приводов главного движения и подач, силовыми
элементами которых являются электродвигатели. В большинстве станков
используются двигатели переменного тока без регулировки частоты вращения.
Вращательное движение ротора двигателя передается на рабочий орган через
многоступенчатую коробку передач для выбора соответствующего режимы обработки.
В некоторых станках используются двигатели постоянного тока с регулированием
скорости вращения. Если при реконструкции или восстановлении привода станка
штатный двигатель постоянного тока находится во вполне пригодном состоянии, то
достаточно только заменить старую систему управления скоростью (не подлежащий
восстановлению преобразователь или систему генератор-двигатель) системой с
управляемым тиристорным преобразователем. При этом двигатель подключается
непосредственно к преобразователю: система ТП-Д (тиристорный преобразователь -
двигатель). Для этих целей хорошо зарекомендовал себя преобразователь
SIMOREG
DC Master 6RA70 производства фирмы SIEMENS. Применение этого
преобразователя позволяет значительно экономить на оборудовании релейных схем и
кабельной продукции. Различные блокировочные связи, управление тормозом,
вентиляцией и смазкой довольно просто реализуется
внутренней программой преобразователя. Для этих
целей у преобразователя имеется достаточное
количество дискретных входов и выходов, которые по
необходимости выбираются опционально, т.е. можно
расширять до необходимого количества. Кроме того, в
преобразователе имеется технологическая программа
со свободно программируемыми функциями, которая
позволяют реализовывать различные схемы
управления механизмами станка и выполнять
преобразования непрерывных сигналов в цифровом
виде. К преобразователю возможно подключение
импульсного датчика частоты вращения, что
позволяет не только организовать обратную связь по
скорости, но и выполнять операции точного позиционирования. Система управления
преобразователем микропроцессорная, обеспечивающая простоту настройки,
диагностику и высокую степень защиты оборудования. Система самопроверки и
диагностики исключает ошибки при вводе оборудования в эксплуатацию, а также
контролирует исправность периферийного оборудования в процессе работы.
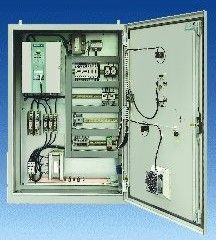
Рисунок №4
    Преобразователи выпускаются на широкий диапазон токов и напряжений, что
позволяет оптимально подобрать оборудование под конкретную задачу.
Преобразователь надежен в работе и удобен в эксплуатации. Применение
преобразователей SIMOREG позволяет к тому же сократить площади занимаемые
электрооборудованием, особенно когда модернизируется привод по системе
генератор-двигатель. Достигается экономия электроэнергии, качество регулирования
выше, чем с применением магнитных или электромашинных усилителей. SIMOREG
легко интегрируется с контроллерами управления, если таковые используются в схеме
станка. Приводы с преобразователями имеют широкий диапазон регулирования
скоростей, что позволяет сократить число ступеней коробки передач, а возможность
формирования кривой разгона с любым желаемым темпом и функцией выборки
люфта, уменьшает динамические нагрузки на механические
части привода, сокращая износ и возможные поломки. На
основе этого преобразователя была проведена реконструкция
привода фрезы продольно-фрезерного станка. Результаты
эксплуатации в течение 2-х лет показали надежность работы
оборудования, релейная схема станка была упрощена.
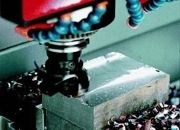
Рисунок №5
    В тех случаях, когда привод станка приходится
укомплектовывать электродвигателями, лучшим
вариантом модернизации является применение
частотного регулирования скорости вращения с
использованием двигателей переменного тока с
короткозамкнутым ротором. Система
управления скоростью двигателей получила
название «
Частотно
Регулируемый
Привод» -
ЧРП.
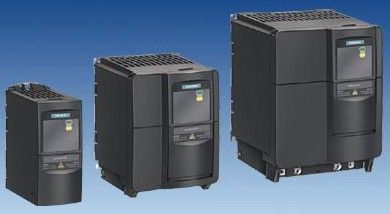
Рисунок №6
    Последние достижения в области производства преобразователей частоты делают ЧРП
одной из самых популярных систем в области регулируемого привода. Современные
частотные преобразователи оснащены микропроцессорной системой управления,
позволяющей осуществить полное векторное управление. Амплитуда и форма выходного
ток или напряжения формируются по принципу широтно-импульсной модуляции. Все это
обеспечивает возможность работы в широком диапазоне частоты вращения приводного
двигателя без применения датчиков скорости (тахогенераторов). Допустимо применение
стандартных двигателей переменного тока без дополнительных фильтров на выходе, так
как форма тока в статоре двигателя близка к синусоидальной. Для особо точных станков
можно заказать и специальные двигатели, которые имеют малую инерционность,
допускают повышение оборотов выше номинальных в 2-3 раза, оснащенные
принудительной вентиляцией, тормозом и импульсным
датчиком, позволяющим измерять перемещения рабочего
органа станка. Возможность форсировки скорости вращения
двигателя в 3 раза исключает применение специального
привода ускоренных подач.
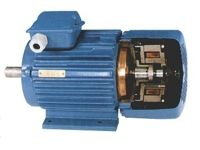
Рисунок №7
    Современный ЧРП по своим статическим и динамическим показателям вплотную
приблизился к приводу постоянного тока, но значительно превосходит его по надежности
и эксплуатационным показателям. Высокий КПД и COS близкий к единице делают
привод экономичным в части потребления электроэнергии. Высокая эффективность
защиты двигателя и самого преобразователя, исключает повреждения и аварии как
электрического, так и механического оборудования.
    
Здесь действует принцип:
«Спроектировал- Купил – Смонтировал – Настроил – Закрыл и Забыл!!!»
    Опыт внедрения частотно регулируемого привода в течение более 10 лет полностью это
подтверждает.
    Так приводы станка для продольной резки рулонного металла полностью выполнены на
ЧРП (разматыватель, привод дисковых ножниц, моталка), достигнута высокая
надежность и качество работы.
    
Станки с ЧПУ. Использование техники ЧПУ одинаково выгодно как в большом
производстве, так и в отдельных мастерских. Начиная с концов 70 годов прошлого века,
машиностроительные заводы начали оснащаться такими
станками, но в основном отечественного производства.
    Механическое оборудование станков и их
металлоконструкции мало изношены в силу того, что они
спроектированы и изготовлены с большим запасом
прочности. Что нельзя сказать об электронном
оборудовании, которое даже у новых станков имело частые
отказы, необходимо было постоянное техническое
обслуживание. Системы ввода информации в основном были
на магнитных лентах, перфолентах и перфокартах, что создавало дополнительные
трудности по составлению программ и наглядности работы. Отсюда можно сделать
вывод, что восстанавливать и ремонтировать старые системы ЧПУ не целесообразно.
Выиграв в разовых затратах на восстановление гораздо больше потеряешь при
эксплуатации, постоянно оплачивая ремонт и дополнительные потери из-за простоев. В
конечном счете, решать заказчику, что ему выгодно на данном этапе.
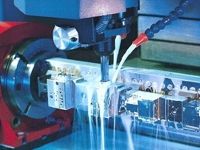
Рисунок №8
    Для каждого случая восстановления надо подходить индивидуально, определяя, что
можно сохранить от старой системы, состояние оборудования, требования к ЧПУ. В
настоящее время предлагаются системы управления, имеющие модульную конструкцию.
За счет этого пользователь может из небольшого числа компонентов быстро и эффективно
собрать свою индивидуальную систему управления для самых различных технологий и
производств.
    Фирма
SIEMENS предлагает единую комплексную систему для ЧПУ, с помощью
которой полностью и эффективно решаются задачи в области высокой
производительности оборудования. Техника автоматизации Siemens определила
совершенно новое видение техники ЧПУ. Система управления предлагает все, что
используется в высоко производительной индустрии.
Это комплексная программа для
самых высоких требований имеет название SINUMERIK & SIMODRIVE и включает:
- SINUMERIK, собственно система ЧПУ с программным обеспечением,
устройствами ввода и отображения (HMI);
- Система преобразователей SIMODRIVE;
- Двигатели SIMODRIVE.
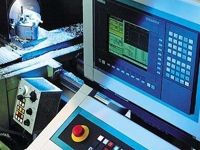
Рисунок №9
    Для каждой задачи устанавливаются подходящие
компоненты, включая системы ЧПУ и привод. С
помощью нескольких модулей, которые имеют
полную совместимость, можно оснащать различные станки. Интеллектуальные системы
для связи человек-машина скрываются в интегрированном модуле РС (SIMUMERIK
PCU), который поставляется в различных вариантах. В
комбинации с панелью оператора ОП SIMUMERIK получается
мощная интеллектуальная система управления и визуализации,
которая имеет небольшие габаритные размеры.
    При наличии большого количества станков с ЧПУ они могут
объединяться по сети, и технолог со своего рабочего места
отслеживает работу всех станков, вводит программы обработки
со своего компьютера на отдельные рабочие места.
    В состав серии входят различные двигатели и системы их
управления.
    За последние тридцать лет влияние числового программного управления на конструкцию
станков привело к появлению совершенно новых моделей станков и механических
автоматов. Сегодня станок с ЧПУ является краеугольным камнем современного гибкого
производства.
    Станки с ЧПУ представляют собой идеальное решение для автоматизации
мелкосерийного или штучного производства. Однако те же станки, объединённые в
гибкие линии, всё больше и больше используются для производства больших серий.
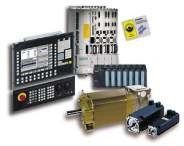
Рисунок №10
    Сегодня заказчику предлагается семейство ЧПУ для простых станков (2 оси + шпиндель
для токарных и 3 оси + шпиндель для фрезерных станков). В качестве приводов могут
быть использованы, как современные шаговые трёхполюсные двигатели (с ЧПУ
SINUMERIK 802S), так и сервоприводы переменного тока с аналоговым интерфейсом (с
ЧПУ SINUMERIK 802C).
    Использование сервоприводов с аналоговым интерфейсом (+/- 10В) позволяет повысить
точность обработки поверхности на тех же станках или же, что является очень
актуальным сегодня на рынке СНГ, использовать ЧПУ SINUMERIK 802C для задач
модернизации станков, причем появляется возможность оставить старые приводы, что
существенно удешевляет модернизацию. При этом всё-таки получается повышение
производительности станка за счёт того, что новая система ЧПУ более надёжна в
эксплуатации, а новые функции ЧПУ позволяют сократить время обработки детали.
    Модификация SINUMERIK 802C позволяет использовать её в качестве простой цифровой
индикации для цифровых станков. Причём её стоимость сравнима или даже ниже, чем
классические системы индикации, существующие на рынке.
    К этим ЧПУ вплотную примыкает система SINUMERIK 802D, которая добавляет ещё
одну ось (например, для управления столом) и работает с универсальным сервоприводом
SIMODIRVE 611U.
    Появление новых функций в ЧПУ позволяет сегодня существенно уменьшить время
переналадки станка, которое в универсальном станке может занимать до 90% от общего
времени работы. Другие функции позволяют избежать поломки дорогостоящего
инструмента и повреждения дорогостоящей детали. Износ инструмента также можно
снизить за счёт программных функций ЧПУ. Повышение качества обработки поверхности
с использованием систем ЧПУ фирмы Сименс позволяет отказаться от финишной
обработки деталей и тем самым не только сократить время производства (т.е. повысить
производительность), но и уменьшить парк дорогостоящих станков.
В течение долгого времени самым большим препятствием на пути быстрого внедрения и
распространения станков с ЧПУ служило программирование. Для написания программ
создавался специальный отдел, в котором работали люди, специально обученные языку
программирования ЧПУ. Было практически невозможно, чтобы даже не очень сложную
программу вводил оператор непосредственно на станке.
    Сегодня фирма Сименс предлагает возможность вводить программу обработки детали в
виде обычной технологической карты. Оператор или человек, вводящий программу
непосредственно на станке, не должен обладать знанием языка программирования. Он
просто вводит по шагам контур детали, состоящий из простых графических элементов,
таких как прямая, дуга, конус и т.д. Все переходы между элементами просчитывает
СЧПУ. Затем моделируются инструменты и траектории их перемещения, а также съём
материала с детали. Каждый шаг поддерживается графически на экране СЧПУ, а в
завершение вы можете получить трёхмерное (или трёхпроекционное) динамическое
симулирование обработки детали. Такое графическое моделирование является настолько
точным, что больше нет необходимости использовать станок в целях проверки. Затем
СЧПУ формирует весь технологический процесс, включая число проходов, выбор
инструментов, скорость вращения шпинделя, скорость подачи и подбор компенсационных
значений. Такая программа может быть оттранслирована в машинные коды и
использоваться в дальнейшем для серии станков. Таким способом можно
запрограммировать в среднем до 90% деталей в любом производстве.
    Таким образом, программирование снова возвращается в цех, что позволяет, с одной
стороны, использовать знания технологии и опыт цеховых специалистов, а с другой - даёт
возможность специалистам из отдела программирования сосредоточиться на оставшихся
10% и работать более эффективно. В условиях кадрового голода такое развитие событий
может принести немалые экономические выгоды.
ТОО «РВСА» ОСУЩЕСТВИЛО РЯД МОДЕРНИЗАЦИЙ МЕТАЛЛОРЕЖУЩИХ СТАНКОВ, А ИМЕННО:
- Продольнострогательный станок, замена привода стола с Г-Д на привод с преобразователем Simoreg.
- Вальце-токарный станок для проточки опорных валков черновой группы горячего стана ЛПЦ1
АО «ArcelorMittal Темиртау». Вес валка Диаметр проточки
Длина бочки В замен привода по системе Г-Д установлен привод с нереверсивным преобразователем
Simoreg на ток 600А. Привод без тахогенератора,
для работы во второй зоне с ослаблением поля разработана специальная программа.
Управление блокировками, обдувом, смазкой и перемещением суппорта осуществляется модулем
«LOGO!» Предусмотрена световая и звуковая сигнализация.
- Фрезерный станок с ЧПУ. Фрезерование сложных конфигураций, рисунков.
- Кординатно пробивной станок, совмещенный с плазменной резкой. Станок
оснащен ЧПУ перемещением по координатам и сменой инструмента.