Research of work of the thyristor drive from twelve pulsing the straightening circuit design
     In powerful direct-current drives for the purpose of decrease in pulsations of voltage
enclosed to propellers they eating from thyristor the converters connected on twelve
pulsing to the circuit design of straightening. Process of switching of the car in this case
improves, distortion of voltage of the feed source decreases.welve pulsing the circuit
design assumes use of two complete thyristor converters, the thereupon from separate
windings of the transformer with voltage phase shift between secondary windings of 30
electrical degrees that increases quantity of pulses of system to 12 for the period. Each
complete device has the system pulsing - phase management, with system automatic
control of key parametres of the drive, protection and signalling system system, etc.
Converters in parallel work on the general loading.
The electric drive circuit design assumes use of one of converters in the capacity of
the leader (Master), and the others - conducted (Slave).
     In the leading converter the control system of the electric drive which starting signal
is the task for a current for own contour of a current, and for contours of a current of conducted devices is realised.
     One-linear ñõ åìà turnings on of converters of type Simoreg DC Master on twelve
pulsing to the circuit design it is presented on picture No 1.
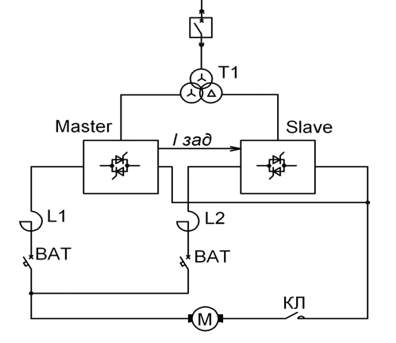
Picture No1
of cold rolling of joint-stock company «Arselor Mittal Temirtau» has been executed. In the
course of drive adjustment insufficiency of dynamic compensation during the initial
moments of dispersal and a retardation, leading to undershootings and tension emissions
on a strip section between the reel and the sixth cage has come to light. Change of options
of correcting links in the course of adjustment have not given expected effect.
Mathematical modelling and research of processes of the drive of the reel has been
applied to the solution of this problem.
     Dynamic processes of the drive of the reel at a shunt connection of converters
proceed originally since even insignificant differences in parametres of an electric chain
and a control system influences dynamics of currents of each converter and, finally, on a total current.
Presumably in investigated system on an error in compensation of a twisting
moment of the propeller the transmission delay of signals from the leader to the conducted converter affected.
     The equivalent circuit diagramme of a power chain of the investigated electric drive is resulted picture No 2.
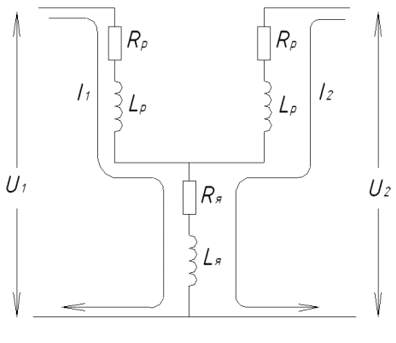
Picture ¹2
Change of electric parametres is presented by the differential equations:
or
Having accepted, that:
L1=Lð - inductance of a smoothing reactor;
L2=Lÿ - inductance of an armature of the propeller;
R2=Lÿ - armature pure resistance;
R1=Lð - reactor pure resistance.
     Proceeding from the equation (2), and the accepted replacement of variables, we
will make mathematical model electric hour òè a controlled process. The model is resulted on picture No 3.
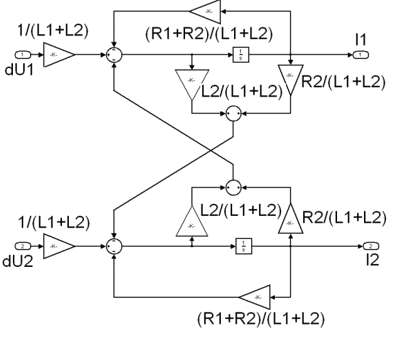
Picture ¹3
Where:
dU1, dU2 - arrival signals, equal differences of feeding voltage and a propeller EMF;
I1, I2 - starting signals - currents of converters.
     Using model of an electric part as compound all system, we model behaviour of the
investigated mechanism at change of speed of a strip. The electric drive model is resulted in picture No 4.
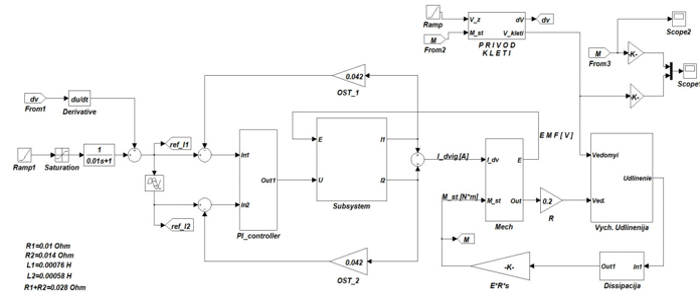
Picture No4
     The model of an electric chain of the propeller is switched on in the block «Subsystem»,
with model thyristor the converters representing deadbeat links of the first order.
     Regulators of a current of each electric drive are presented by block "PI_controller".
Scaling of return couplings on a current of wasps óùåñòâëÿåòñÿ blocks "OST_1" and «OST_2».
     Dynamic compensation of a tension at change of speed of a cage is executed by the differentiation block «Derivative».
     Delay in a signal transmission is carried out by the block «Transport Delay». The
model of a mechanical part of the electric drive is executed in subblock "Mech".
     Strip model on a section from the sixth cage to the reel, it is realised in the block «Vych. Udlinenija».
     The cage model represents the electric drive of infinitely high power, is realised by the block «PRIVOD KLETI».
     Modelling was spent by different magnitudes of delay of a signal transmission of the
task of a current to the conducted converter.
     In picture No 5 oscillograms of change of a tension in a strip are presented at
various delay in a signal transmission of the task of a current.
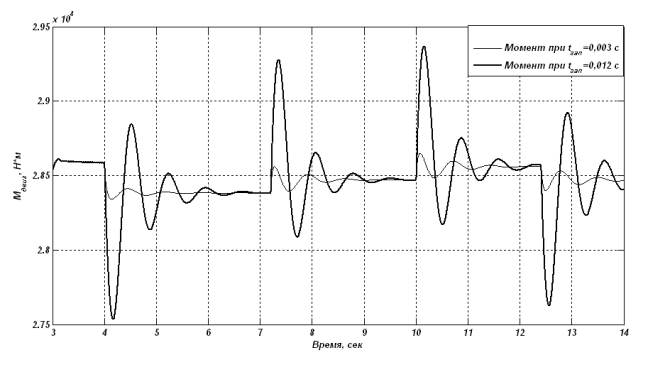
Picture No5
     Oscillograms of currents of the electric drive are shown in picture No 6.
     The analysis of oscillograms of a current:
     In a time span1
for the overhead drawing, and t2 - for bottom, one of currents decreases
rather its previous value in spite of the fact that the signal of dynamic compensation is
directed on increase in a current for the purpose of lead angle of dynamic losses a little.
Current decrease occurs because of a signal time delay. The matter is that for the time
delay account.
     Signal the current of the first converter increases more sweepingly, increase
against- the EMF for the second converter, that naturally leads to decrease of its current.
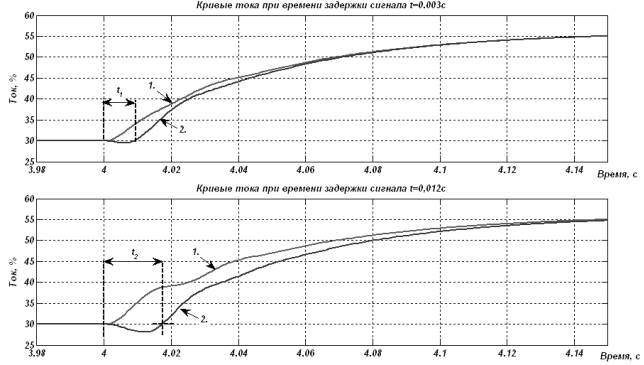
Picture ¹6
     During this period the total moment of the propeller more low, that leads to tension
decrease by a section (picture No 6). Result of an undershooting of a tension is a number
of damped vibrations of an elastic-system.
CONCLUSION
     The moment deviation on the shaft of the propeller of the reel in transitive regimes
on speed because of delay in the channel of transfer of the task of a current on ñamps for
thin sheets when the general tension of all of hundred kg, this deviation makes negative
impact on quality of metal because of originating dynamic blows, and in some cases can
lead to strip gusts. To eliminate this problem it is possible having increased speed of
signalling to greatest possible.