Kok Tobe rope way drive control system
     Customer: “Park Kok-Tobe”, Ltd., Almaty
RECONSTRUCTION OBJECT SPECIFICATION
     Ropeway Kok Tobe is placed into commission in 1976; in 2005 it was offered the reconstruction of automatic control
system by the ropeway drive. Before the reconstruction the ropeway drive was morally out-of-date system, constructed on relay contact circuits.
A wound rotor induction motor with power 100 kWh is used as a master drive, permitting to work in speed range from 1 to 6.3 mps.
Speed control was carried out with the help of resistance measurement in the rotor circuit and had 5 stages in each side. For ropeway work
in the preventive measure and repair, a cage induction motor with power 14 kWh was foreseen, allowing to move at a speed of about 0,5 mps.
Over a distance of the latest years automatic mode of drive working wasn’t in operation, ropeway control was carried out by hand.
Requirements to control system
- It is necessary to provide set speed of carriage movement.
- To provide carriage soft start and breaking.
- To provide accurate carriage stop as automatic so manual.
- To output movement parameters on the operator’s panel.
SOLUTION AND AUTOMATION SYSTEM CHARACTERISTICS
     The frequency drive of the firm Siemens Sinamics S150, the controller CPU S7-300 313C-2DP and operator’s touch panel
Simatic TP270-10 were chosen for received technical task realization. Absolute value sensor ‘Simodrive sensor’ was used for carriage way determination.
Connection between operator’s panel the controller, the drive and way sensor is carried out by PROFIBUS-DP.
     Optical sensors BERO are used for accurate carriage arrival to the station and automatic correction of
determined carriage way (spring compensation during road commission and temperature effect). During the reconstruction some
changes were made in kinematic chain; in this case safety locks and stops chain is saved. Available service break was dismantled due to the fact,
that a new motor of Siemens was dismantled due to the fact that new motor of Siemens with power 160 kW had optically in-built electro-magnetic
plate brakes with manual release function.
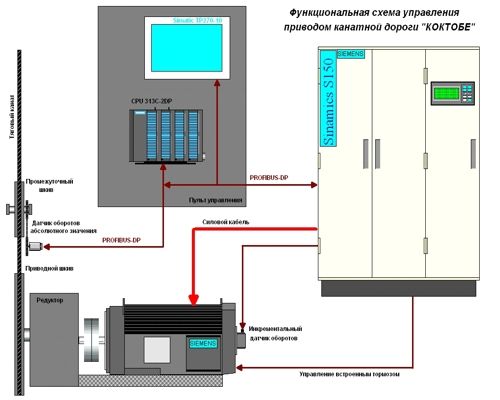
Picture No1
     New operator’s pulpit not only changed its size but it became more compact;
Carriage movement control saved operator’s procedural path because of it operators could work with new control system without any problems.
At the same time, after modernization some buttons on the pulpit were deleted, because they became needless.
Operator’s actions at system assembly are blocked up with buttons ‘emergency stop’, ‘drive demounting’,
carriage movement joystick is not zero position and key tag is in prohibiting position. Conditions of the drive, interlock circuits,
warning and carriage position can be watched on the operator’s panel.
     Operator’s panel has several windows. The window “Operator” serves for visual display of drive conditions,
carriage movement speed, drive current, carriage movement direction, carriage positions and carriage distance concerning to the upper station.
When frequency drive Sinamics S150 was implemented, control system permits to carry out speed task directly from the operator’s panel.
There are two drive work modes for the ropeway. This is Working mode, permitting to work at speeds which are equal to working ones
(full speed is 6, 3 m/sec) and Switching mode, permitting to work at low speeds without working mode change.
Minimum speed, at which the ropeway works after drive modernization, is 0,05 m/sec. and maximum one is 7 m/sec.
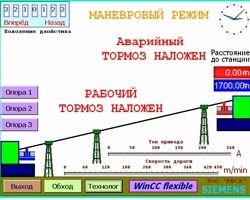
Picture No2
     It’s possible to select the window Support on the operator’s panel,
where you can consider carriages arrival to the concrete Support place.
Moreover, carriage distances to the station, drive current, direction of carriage movement,
carriage position on the support and carriage driving speed are displayed either in operator’s window or in support window.
It’s possible to enter in the bypass window from any windows, here it is observed readiness of safety lock chain and in
the case of carriage overwind and runover on emergency limit switch, in this window it was
foreseen emergency interlock bypass by one from limit switches for carriage cross over from emergency limit switch.
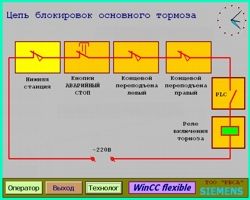
Picture No3
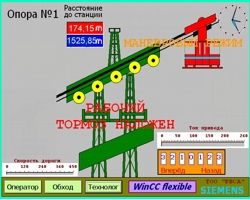
Picture No4
     Also it is possible to exit in the window Technologist from any window.
It’s possible to look through required speed modes for the Working mode and Switching mode,
also to change actual mode. From the window Technologist there is exit in additional window,
where it’s possible changing of speed mode, manual zero filling of carriage position, counter device of
journey number and interlock speed bypass function for adjustment.
     After modernization of ropeway drive control system all sound and lamp signaling were realized according
to the commission requirements. In accordance with technological task, control system provides soft carriage arrival
and departure from the station in the automatic mode, but an operator has control priority, he can take control on himself at any time.
Until modernization heating of ballast resistors in the circuit network during drive movement, it led to additional losses of electric energy.
Using of the modern frequency converter Sinamics S150 on this drive with the recuperation possibility permited
to reduce active power consumption and to stabilize reagent, because cosine is installed in the compensation mode which equels 0,96.
Using of additional switching motor during preventive measure and repairs on this system became illogical.
Therefore switching motor is used in emergency cases at energu tripping and the work from field ion source.
Project implementation period
     Project implementation period is 4 months, commissioning is May, 2006.