Modernization of electrotinning line 1200/III control system
     Customer: JSC “Mittal Steel Temirtau”
ÎÏÈÑÀÍÈÅ ÎÁÚÅÊÒÀ ÐÅÊÎÍÑÒÐÓÊÖÈÈ
     The electrotinning line - 1200/III is destined for tin coating on the surface
of the steel cold strip by electroplating technique. Final product is tin production for food industry.
     The electrotinning line includes the following areas:
- Inlet area
- Chemical area (middle area)
- Outlet area
- Cutup line
- Stretch straightening machine
- Radioisotope thickness gage for sectioning.
- Sheet sorting machine (line).
- A chemical underground store room (solvents and reagents preparation).
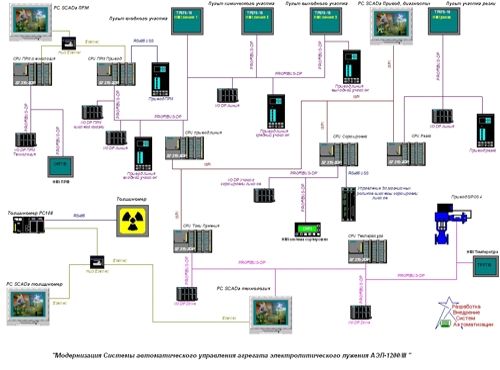
Picture No1
Requirements to automation system
- It is necessary to classify a machine under local systems.
- To save blockings and to organize emergency messages recording.
- To change operator’s mnemocircuit on visualization on the basis of PC and OP.
- To save tinning current diagram according to the all baths during the month.
- To provide step-by-stem system implementation without long-time stop.
- To connect local systems between systems for data exchange.
SOLUTION AND AUTOMATION SYSTEM CHARACTERISTICS
     It was decided to allocate eight local automation areas for operating staff comfort.
- Drive and line transportation chain control system
- Tinning current control system
- Tension-leveler control system, drive.
- Tension-leveler control system, technology.
- Solvent temperature control system.
- Cross cutting line control system.
- Sorting line control system.
- Radioisotope thickness gage control system.
     Electrotinning line control system is implemented on the basis of seven independent
(local) PLC (Simatic S7-300) and a controller on the basis of ÐÑ104 (thickness gage).
All elements of control system are connected with their decentralize circumference by busbar Profibus-DP,
whereas systems are connected between them by MPI, PROFIBUS and Ethernet.
     Visualization system includes four pulpits, situated on the line, equipped operator’s panels ÒÐ 270-10,
six operator’s panels ÎÐ73, situated on the sorting line, two operator’s panels on the sheet-leveler, one operator’s panel
in the chemical underground store room. Also visualization is carried on the basis of PC: the first station combines
diagnostics and condition for drive and cutting line, the second station combines tinning current area and solvents temperature
in the chemical underground store room, the third station is tension-leveler technology and the fourth station is radioisotope
thickness gage. Tinning line control is carried out from three pulpits: inlet, outlet and chemical area.
Cutting line control is carried out from another pulpit.
     Operator’s sensor panel TP270 is destinied for displaying of technical process condition,
also for electrolyte tinning line condition control. Developed graphic structure of OP on the basis of WinCC-flexible,
allows an operator to control working modes, to watch and react on all emergency and pre-emergency conditions of line electric drives,
also to control line technological parameters.
     All information is brought to the PC station for all technological process control and reacting
at the moment of emergency situations. OP is developed on the basis of WinCC V6.0.
Project implementation period
     Project implementation period is 11 months, commissioning is November, 2007