Process parameters control and regulating system in Lime shop
ËLime kiln line consists of four main units: lime kiln, cooler, 2 skip elevators and heat recovery boiler.
Rotating kiln (RK) - counterflow heat exchanging unit with length 75m and diameter 3.6m, capacity 300t/day. Furnace is driven by a motor with phase rotor via four-step gear box. Kiln rotation speed varies from 0.66 to 1.34 rpm. Material calcining is made with help of a heat generated from black oil or its alternative burning. Fuel supply regulation is carried out with help of valve dia. 25mm with electrical actuator.
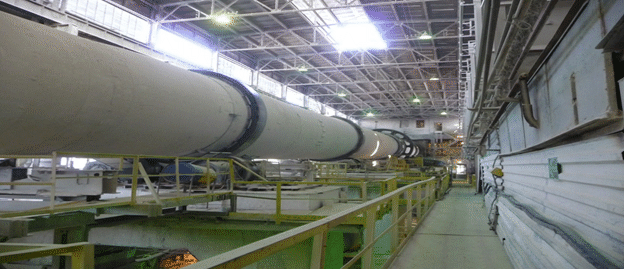
Figure 1
Heat recovery boiler HRB-60 is installed behind the lime kiln and destined for steam generation, utilizing the heat of exhaust gases. Single-drum coiled boiler with multiple forced circulations has vertical gas duct location and horizontal coil pipe location. Boiler layout is flat-topped. Steam superheater and the package of the second evaporative section are located in the vertical gas duct. Water level in the boiler is supported with help of multipurpose valve dia. 32 mm, installed at the feedwater pipe.
Skip elevators are destined for final product transportation from cooler output to storage bins.
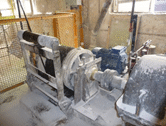
Figure 2
Power part of the drive consists of cable winch, cylinder-shaped gear box, rotary-field motor with square-cage rotor and electrohydraulic brake.
“RVSA” Ltd. has developed, mounted and implemented visualization, monitoring and control system of line work. Total scope of work was carried out on turnkey basis with equipment and software product supply.
Material temperature control in the kiln was carried out in three zones with the help of measuring devices «Wtrans B» from the firm JUMO with distant wireless data transfer through the protocol Hart Wireless. Special inset constructions with transmitter protection from heat radiation of the kiln were made and mounted for temperature sensor installation.
The temperature of final product at the entry from cooler is measured in intermediate storage bin.
Temperature and vacuum are measured around the gas circuit.
Coriolis acceleration flowmeter Endress&Hauser Promass 40 was used to determinate fuel consumption, which additionally measures tightness an temperature of passed product through it.
Air consumption for burner is measured with the help of vortex flowmeter Endress&Hauser Prowirl 72.
Total air consumption on burning is determined with the help of measuring diaphragm and device dTRANS p02 DELTA from the firm JUMO, in the same way water and steam consumption at the heat recovery boiler is measured in the same way.
Total cooling water consumption is controlled by electromagnetic flowmeter Endress&Hauser Promaq 10. Special constructions with installed sensors are provided for temperature measuring of water at the discharge from rotating supports of the kiln.
Special unit with linear displacement transducer was developed and made to control kiln axial displacement. Kiln rotation speed is determined according to rotor current frequency with the help of device, developed and made by “RVSA” Ltd.
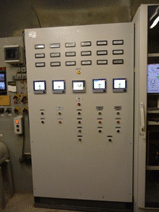
Figure 3
Heat bearing control of rotating supports is realized.
Paperless recorders «LogoScreennt» are used as secondary devices with TFT-display, CompactFlash-card and USB-interface, interconnected with each other and Modbus TC based server. The devices are installed on panels located in operators' room VP-3 and heat recovery room. As well signal devices and control elements are installed at these panels.
Developed SCADA system in visual form displays condition of equipment and industrial process. Availability of process parameter schedules and message archive allows analyzing production for a long time period. 23’’ monitor uses for parameter visualization of technological process in a convenient form for kiln and boiler operators.
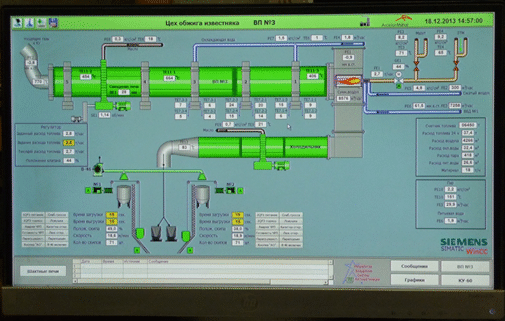
Figure 4
Automatic control of fuel consumption is carried out; therefore compact microprocessor controller «IMAGO 500» of JUMO is used, which in combination with frequency converter «ACS-150» operates by conveying speed of control elements. Using of the frequency converter improves regulatory quality and considerably prolongs operation of the actuator and the regulating valve.
Automatic level water control in the drum of the heat recovery boiler is carried out in the same way.
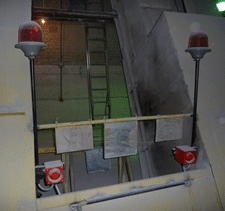
Figure 5
Warning, emergency and prestart signaling system provides facility security, operation safety and excludes breakdown in process.
Signaling system consists of audio and light devices and light panels on the switch-boards.
Electric drive control system of skip hoists
Electric drive control system of skip hoists âûwas carried out with using of microprocessor technology: PLC«Simatic S7-300», «CPU-313C-2DP» and frequency converter «ACS-800», made by ÀÂÂ.
Drive control from frequency converter allows providing desired speed diagram of skip hoist work. Dynamic loads to the motor and mechanical units were reduced as a result of frequency regulated drive implementation. Frequency converter control system carries out all required motor and cable line protections.
Control system provides:
- required interlocking;
- calculation of skip current position;
- transmission in upper level control system of skip position;
- discrete signal transmission about condition of control system (work/accident).
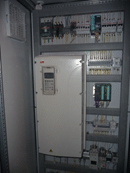
Figure 6
Equipment of electric drive and each skip control system is located in the cabinet with IP55 level sealing protection, equipped by forced ventilation with automatic temperature switch-on.
Frequency converter is fitted with brake unit and resistor that ensure braking energy degradation.
Absolute encoder is installed in order to determine current position of the skip. Discrete proximity sensors of uppermost and downmost skip position ensure correlation of determined position with true coordinates. Limit switches are used in interlocking system: «gate», «hatch», «material overflow trap», «skip overwinding», «slack in the wire».
There is a manually actuable control for skip hoist. Keys and LED button switches, alphameric displays are installed; it ensures convenient control and diagnostics.
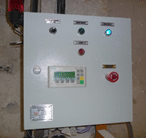
Figure 7
System works in automatic and manual (adjustment) modes, therefore local control units are installed at charging and discharging.
Speed modes and charging and discharging periods can be installed not only with the help of local control units but also with operator AWS of the kiln.